在钢管、型钢等产品的生产过程中需要锯切定尺,产品端部会产生锯切毛刺,对产品的外观、质量等均有较大影响,因此打磨去毛刺已成为生产过程中的重要工作。
目前,国内各钢厂的去毛刺工位以人工为主,其劳动难度大,去除效率低、工作环境差,且只能靠目测和感觉操作,去毛刺质量难以保证。以柔性力控为核心技术的机器人自动打磨去毛刺系统。系统主要由工业机器人、柔性去毛刺单元、3D视觉系统、控制系统等组成。柔性去毛刺单元可按产品形状设置打磨路径,降低编程难度,如同人手一般进行柔性控制,减少工件定位造成的误差,从而保证产品打磨的一致性,有效保障产品质量。
一、人工去毛刺现状
1. 劳动难度大。人工对不规则的产品去毛刺,很难保持一致性;
2.工作危险高。现场比较混乱,安全隐患严重;
3.工作效率低。人工去毛刺,最多一天工作十小时左右,速度慢,大毛刺需反复清理,效率低下;
4.工作环境差。打磨所产生的大量粉尘,对身体伤害严重,容易引发职业病。
二、机器人去毛刺系统的优势
1.可针对毛刺类型选取不同设备,兼容性高,适合智能制造柔性生产;
2.与人工相比,通过改进工艺,耗材减少,效率增加;
3.工业机器人不疲劳,实现连续自动化作业、产量稳定;
4.工业机器人不马虎,产品质量稳定性提高,不会出现缺漏现象;
5.工业机器人不挑剔,绝对服从管理;
6.不同工位按工作需要启动设备,节约能源。
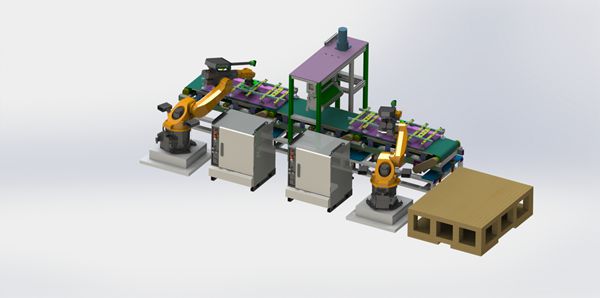
三、设备特点
1.机器人去毛刺打磨单元具有占地小、生产高效、通用性强、安静环保等特点。
2.机器人去毛刺打磨单元采用国际知名机器人、专业的去毛刺打磨工具、集尘、铸件输送于一体的自动化去毛刺打磨集成单元。
3.根据铸件毛胚的特点和去毛刺打磨的产能需求,可以提供单台、多台机器人抓工具或抓铸件,以及双工位、连续式、中央式的铸件输送的解决方案。
四、设备使用范围
1.机器人去毛刺打磨单元使用于中小型压铸件,实现各类铸件的去毛刺、表面打磨等功能需求。
2.通过自动化、智能化、与模块化的去毛刺技术整合,为客户解决去毛刺改革困境,产品品质提升难点,实现生产效率最大化,以及环境保护等综合企业技术提升的良好助力。
|